Overview
For this assignment, we had to find a free-to-print model of an “impossible” object to 3D print. The object had to be small enough to fit in a gumball machine capsule, and we needed to print 5 of them after trying at least 2 different 3D printing techniques. I chose to print a little army of little sharks, waiting to be freed from their plastic prisons.
Shark Spotting
Before checking out the 3D printers, I went to Thingiverse.com and found a design for a flexible, articulated hammerhead shark. This shark is meant to be a “print-and-play” piece, meaning that no supports or filing should be needed, and the model will move once you take it off the plate. This is due to the internal interlocking joints, a factor that makes this piece “impossible.” At first, I wanted to do a print of Dwayne “The Rock” Johnson’s head, but this would probably not have been intricate enough to be considered an “impossible” object for the purposes of this homework.

The design I originally wanted to print.
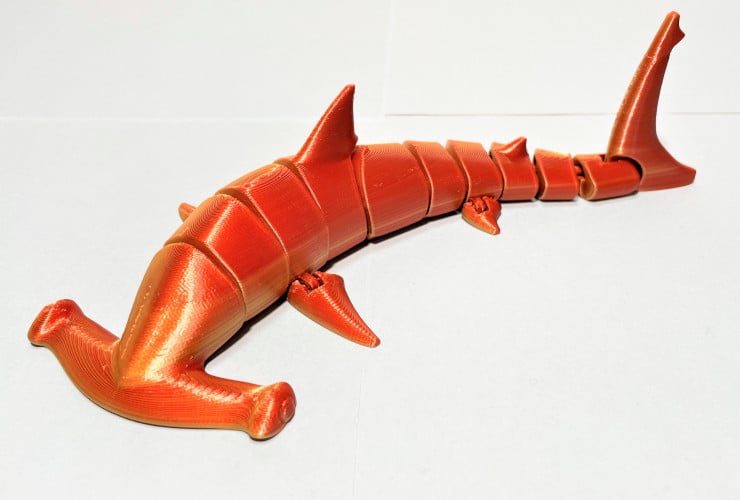
The design I went with.
FDM Test Print
I downloaded the zip file from the website and chose to print V3. I moved this file to my USB drive, then took it to the OEDK MakerBar computer. Due to the glowing reviews of the Bambu printers we heard in class, I decided to try those FDM machines first. I imported my file to the slicer software and set the scale so that my shark would be 50 mm long. I then sliced the model, setting the layer height to 0.11 in hopes that the smaller layer height would help with the small details. I then sent the file to the printer. This whole process was very simple, only taking about 5 minutes from plugging in my flash drive to the printer starting up.

Shark attempt 1 in Bambu Studio

A livestream of the inside of the printer via Bambu Studio.
20 minutes later, I checked on my baby shark. The print had some issues around the tail, probably because the Bambu prints very fast, and the tip of the tail is very small. The 50 mm shark fit very easily into the gumball machine capsule without bending, but when I tried bending it to test the movement, the body broke.
To hopefully increase the strength of the joints, I increased the scale to 60 mm. I also decreased the layer height from 0.15 to 0.11 mm and the initial layer height from 0.2 to 0.15 mm. Unfortunately, I still saw an issue with the tail. The shark fit into the capsule with slight bending, so I scaled up the print again.

Shark attempt 2 in Bambu Studio.

Tail close-up.
Assured that the third time would, in fact, be the charm, I printed a trio of 75 mm sharks. One of the sharks disappeared (was not in any of the bins), another shark’s tail turned out to be a little lumpy, but the third turned out perfectly. Unfortunately, I was not very careful while testing out the movement and ended up snapping off the tip of the tail. Regardless, the settings I had worked well.

Shark attempt 3 in Bambu Studio.

75 mm shark twins.
I tested these same settings on a Prusa machine. After opening the PrusaSlicer software, the only change I made was the addition of a brim to increase print stability. Because the Prusa machines required an SD card to receive the file instead of the Bambu software that does it through the cloud, the process to load the print to the machine took a bit longer. The Prusa also printed much more slowly than the Bambu.

Prusa printer.

First layer on Prusa with brims.
After 4 hours, I came back to find 3 beautiful baby sharks. Sadly, one of their heads fell off while I was trying to remove the brim. I then dropped another, causing it to break in half. Perhaps someone should have called shark protective services on me at this point. I kept the third intact shark safe in a plastic capsule from this point forward.

R.I.P. right shark.

Photos taken seconds before tragedy struck (I dropped one of the sharks).
SLA Test Print
After perfecting the settings for the FDM machines, I wanted to test an SLA print. On the same computer I had been using previously, I opened the PreForm software and followed the directions outlined in the homework document to print my piece. The directions said to automatically orient the model and add supports, which I realized later might have been a bad idea. Because SLA prints an entire layer at a time, it should be quicker than the FDM. However, because only the “tough” resin was in use, which seems to take much longer to cure/print, my single 75mm shark with supports took 2.5 hours.

FormLabs SLA Printer.

75 mm shark after automatic orientation and support generation in PreForm software.
After taking out my print, I washed it and proceeded to trim the supports before curing. I was told by some of my classmates that, with this resin, the supports become close to impossible to cut off after curing. I removed the supports and tried to wiggle my shark around. The shark didn’t bend, and instead ended up breaking. I believe this is because the automatic support generation interfered with the complex internal geometry of the joints, preventing them from moving the way they were designed to. This makes sense considering the print-and-play pieces are not supposed to be made with supports. I decided not to cure my broken shark. Another casualty.

A broken shark, freed from its supports.

Fracture close-up.
FDM Final Print
Since the SLA print turned out to be a) immobile and b) very slow to produce, I decided to get my total of 5 sharks through FDM. I re-ran the model on the Bambu so I could get a total of 5 sharks with good tails. I also added two of Linda’s objects to make the most of the 3D print time.

Final prints in Bambu Studio.

First few layers in the printer.
This time, I was much more careful about how I handled them coming off the printer. I safely placed each shark in a capsule with a strip of paper detailing the user (me) and the link to the 3D model on Thingiverse.

Shark eggs, complete with paper strip. Also technically my last used workspace as I cut the paper and encapsulated the sharks here. Cleaning up after printing just consisted of taking the prints off the print bed, removing extra extruded PLA, and returning the sheet to the printer, so taking a photo of an empty 3D printer felt weird.
Cost Model
Cost Type | Cost | Price | Source | Quantity | Total |
Materials | PLA Filament (white) | $11.99 /kg | Amazon | 50 g | $0.60 |
PLA Filament (grey) | $11.99 /kg | Amazon | 15 g | $0.18 | |
SLA Tough 2000 Resin | $149 /L | FormLabs | 5 mL | $0.75 | |
2 Inch Toy Capsules | $35.99 /150 capsules | Amazon | 5 Capsules | $1.20 | |
Paper | $7.41 /500 sheets | Amazon | 1 Sheet | $0.01 | |
Labor | 3D Print Operator | $21 /hour | ZipRecruiter | 2 Hours | $42 |
Prototyping Engineer | $3.49 | Etsy | 1 Download | $3.49 | |
Overhead | Makerspace Access | $40 /month | The Maker Barn | 3 Days | $40 |
Total | $88.23 |
For the prototyping engineer, although the total printing time totaled about 8 hours, very little of that was active “operating” time. In reality, I only spent about an hour in total in the OEDK setting up the prints and then taking them off the printers. However, I did have to bike to and from the OEDK a few times, so I’ll count it as a total of 2 hours of labor. I have never made a model as complex as this one in CAD. Therefore, I could not estimate how much time it might have taken the original designer to produce the shark model. Instead, I found their Etsy and pulled up the cost of the 3D print file. The version on Etsy is licensed for commercial use, so if we wanted to theoretically sell these sharks, we would be able to after purchasing this file. As with previous cost analyses that included the overhead cost of a makerspace, I will include the charge for the whole month despite only going in for 3 days since membership is charged monthly. As expected, the main costs of this project were labor and overhead. The cost of materials and the file were only $6.23 for 10 prints.