Group Members: Eva Montenegro & Yimo Gao
For the midterm, we decided to do the simple model, taking inspiration from the Dancing Flowers Machine. Like this model, our project was based on Mechanical Movement #96: the heart cam. Rotating the cam around its center axis causes the cam to impart a horizontal force onto a follower, moving the follower away from and toward the cam.
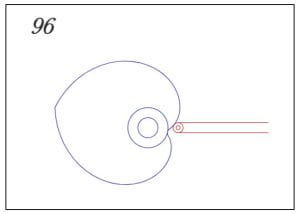
Movement #96
For our machine, we wanted to make three fish move up and down, so we flipped the cams and followers to create vertical movement. After reading about the past engi students’ experience with the heart cam, we also decided to opt for a different cam shape. Our original cam design was a bean-like shape to create non-uniform up and down motion. We also used en.makercase.com to generate the 2D drawings for a box to hold our cams and shafts, as well as a background piece to stand on top of the box.
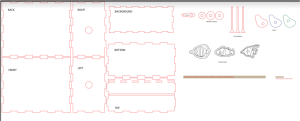
2D drawing
After discussing our original design with the engi teaching team, we decided to make holes to hold each individual follower as well as add a second horizontal layer inside the box to help stabilize the followers. We also decided to double up the cams and followers to create a larger contact surface area between the two and allow for a better transfer of force.
To create our low fidelity prototype, we used the laser cutter to cut out the box pieces and one set of cams and followers out of cardboard. When we tested out the original design, the corners of the follower’s triangle feet would get caught in the dip of the cam, preventing full rotation of the cam. To fix this, we rounded the corners of the feet. Unfortunately, the followers still got stuck because the dip in the cam shape was too deep. After trying and failing to get it to work with a shallower dip, we removed the dip completely and opted for an egg-shaped cam. With this new cam shape, we were finally able to fully rotate our mechanism.
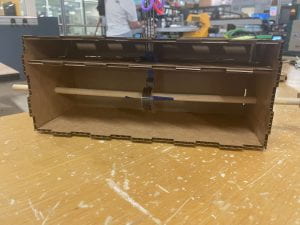
1st low fidelity prototype
After we got our cam mechanism to work, we decided to add a foreground wave that we would also try to move up and down. To achieve this, we added front slots into the two layers of our box to hold the legs of the waves. We then added long and skinny cams that acted like little arms reaching out to the legs of the wave to pick up and drop the wave. When we tested this out with cardboard, we realized that the cardboard arms were too flimsy to hold up the wave. Since we had already gotten the cams to work, we decided to create a higher fidelity prototype out of wood, hoping that the stronger material would help us get our waves to move.
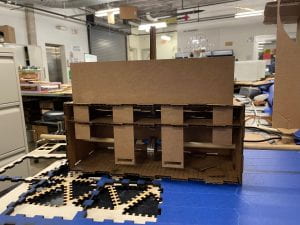
2nd low fidelity prototype with wave
We used the laser cutter to recut all of our pieces out of wood and then assembled our prototype. Like the cardboard version, our cam and follower mechanism worked. However, our waves were less successful. Although the wooden arms could now hold the wave without bending, there was too much friction between the slots and wave legs to get the wave to move up and down. To fix this, we decided to reduce the number of legs from 4 to 2 and to cut the wave out of acrylic in order to minimize friction.

1st wooden prototype
Cutting the wave was the first time either one of us had laser cut acrylic. For our first attempt, we used a really thin piece of acrylic, which resulted in some major warping. The warp in the wave caused it to get stuck in the slots, preventing up and down motion. To try and reduce warping, we recut the wave using a thicker piece of acrylic and adjusted the size of our slots accordingly. Fortunately, this did remove most of the warping and our prototype successfully moved the wave up and down.
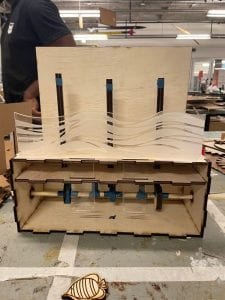
prototype with acrylic wave
Once we had everything moving correctly, we laser cut our three fish. We also used the waterjet cutter to cut out a metal handle to make rotating the shaft easier. We sandblasted the handle to make sure it had a smooth finish.
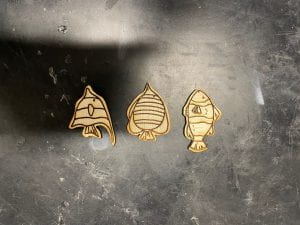
laser cut fish
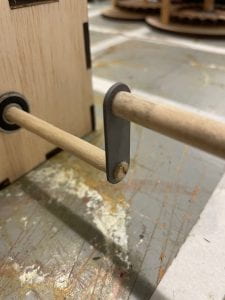
waterjet cut metal handle
To create our background, we used the vinyl cutter to make a vinyl sticker of some waves and underwater plants. After using transfer paper to place the sticker onto our background piece, we spray painted the piece, creating a light to dark blue gradient to mimic the ocean. We then removed the vinyl sticker to reveal our image. It turned out really cool!! After sanding our wooden pieces, we also used tung oil to finish all other wooden parts of our machine.
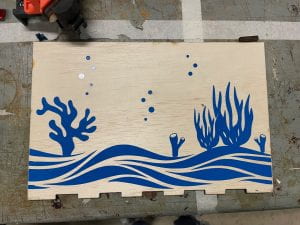
vinyl cut sticker

spray paint over vinyl sticker
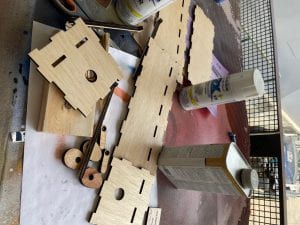
finishing with tung oil
After finishing all of our pieces, we put everything back together and tested it again to make sure it still worked. And our ENGI 210 midterm was finished!!!
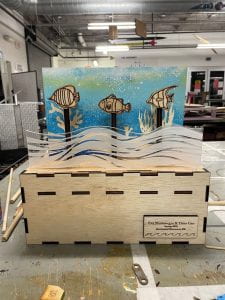
finished midterm project 🙂
Clean Workspace:
Cost Analysis:
Blueprint | |||||
Cost | Price | Source | Quantity | Total | |
Design | Engineering and Development | $37/hr | ZipRecruiter | 1 hr | 37 |
Technical Illustrator | $28/hr | ZipRecruiter | 2 hr | 56 | |
Sum | 93 | ||||
Low& Mid Fidelity Model | |||||
Cost Type | Cost | Price | Source | Quantity | Total |
Materials | 48 x 96″ Corrugated Cardboard Sheets 32ECT 250/SKD | $4.83/ sheet | BenchMark | 1/5 | 0.97 |
3M 2090 Painter’s Masking Tape – 2″ x 60 yds | $9.95/ roll | ULINE | 2/72 | 0.28 | |
3/8 in. x 48 in. Raw Wood Round Dowel | $1.26/ piece | HomeDepot | 15/48 | 0.39 | |
Labor | Laser Cutter Operator | $19 /hr | ZipRecruiter | 2 hr | 38 |
Prototyping Engineer | $36 /hr | ZipRecruiter | 1 hr | 36 | |
Overhead | Facility Cost (Machine Time) | 12.73/hr | AlphaLazer | 1.5 hr | 19.10 |
Design | Engineering and Development | $37/hr | ZipRecruiter | 1 hr | 37 |
Technical Illustrator | $28/hr | ZipRecruiter | 2 hr | 56 | |
Misc. | Waste and Scrap | $4.83/ sheet | BenchMark | 1/4 | 1.21 |
Sum | 188.94 | ||||
High Fidelity Model | |||||
Cost Type | Cost | Price | Source | Quantity | Total |
Materials | 2’x2’x1/5” Plywood | $7.28/ piece | Home Depot | 3/2 | 10.92 |
3M 2090 Painter’s Masking Tape – 2″ x 60 yds | $9.95/ roll | ULINE | 2/72 | 0.28 | |
3/8 in. x 48 in. Raw Wood Round Dowel | $1.26/ piece | HomeDepot | Reused | 0 | |
Labor | Laser Cutter Operator | $19 /hr | ZipRecruiter | 1 hr | 19 |
Prototyping Engineer | $36 /hr | ZipRecruiter | 1 hr | 36 | |
Overhead | Facility Cost (Machine Time) | 12.73/hr | AlphaLazer | 1 hr | 12.73 |
Design | Engineering and Development | $37/hr | ZipRecruiter | 0.5 hr | 18.5 |
Technical Illustrator | $28/hr | ZipRecruiter | 2 hr | 56 | |
Misc. | Waste and Scrap | $4.83/ sheet | BenchMark | 1/5 | 0.97 |
Sum | 154.39 | ||||
Final Product | |||||
Cost Type | Cost | Price | Source | Quantity | Total |
Materials | 2’x2’x1/5” Plywood | $7.28/ piece | Home Depot | 3/5 | 4.37 |
16 Gauge 15” x 12”x 0.06″ Cold Rolled Steel Sheet | $10.8/ piece | WeldMetalsOnline | 9/2500 | 0.04 | |
3/8 in. x 48 in. Raw Wood Round Dowel | $1.26/ piece | HomeDepot | Reused | 0 | |
Gorilla Wood Glue Natural Wood Color, 4 ounce Bottle | $3.47/ bottle | Walmart | 17/1000 | 0.06 | |
12″ X 12″ X 0.118″ Acrylic Sheet Clear | $7.61/ piece | OnlineMetals | 3/5 | 4.57 | |
Watco Tung Oil Clear, 1 Quart | $27.97/ can | Walmart | 53/1000 | 1.48 | |
12 oz. Gloss General Purpose Spray Paint | $6.48/ can | HomeDepot | 1/5 | 1.30 | |
Blue Permanent Vinyl – 12″x11FT Blue Adhesive Vinyl Roll | $6.99/ roll | Amazon | 13/250 | 0.36 | |
3M SandBlaster Pro Very Fine Sheet Sandpaper 9-in W x 11-in L | $1.396/ sheet | Lowes | 1 | 1.40 | |
Labor | Laser Cutter Operator | $19 /hr | ZipRecruiter | 0.75 hr | 14.25 |
Water Jet Cutter Operator | $16 /hr | ZipRecruiter | 0.75 hr | 12 | |
Wood Finisher & Artistic Design | $27 /hr | ZipRecruiter | 1.5 hr | 40.5 | |
Overhead | Water Jet Cutter Operation Cost | $19 /hr | TechniWaterJet | 0.5 hr | 9.5 |
Laser Cutter Operation Cost | 12.73/hr | AlphaLazer | 0.5 hr | 6.37 | |
Other Machine Time | $65/hr | Woodweb | 0.25 hr | 16.25 | |
Quality Control | $37 /hr | ZipRecruiter | 0.5 hr | 18.5 | |
Design | Engineering and Development | $37/hr | ZipRecruiter | 0.25 hr | 9.25 |
Technical Illustrator | $28/hr | ZipRecruiter | 0.75 hr | 21 | |
Misc. (Scrap) | 12” x 12”x 0.08″ Acrylic Sheet Extruded Clear | $13.60/ piece | OnlineMetals | 3/5 | 8.16 |
3M 2090 Painter’s Masking Tape – 2″ x 60 yds | $9.95/ roll | ULINE | 2/72 | 0.28 | |
16 Gauge 15” x 12”x 0.06″ Cold Rolled Steel Sheet | $10.8/ piece | WeldMetalsOnline | 9/2500 | 0.04 | |
2’x2’x1/5” Plywood | $7.28/ piece | Home Depot | 7/16 | 3.19 | |
Sum | 172.84 | ||||
Summary | |||||
Cost Type | |||||
Materials | 26.40 | ||||
Labor | 195.75 | ||||
Overhead | 82.44 | ||||
Design | 290.75 | ||||
Misc. (Scrap) | 13.83 | ||||
Total | 609.17 | ||||