As a wise tea barista once told me, in tea joints and in T-joints, the most important thing is to avoid burning.
Let’s begin.
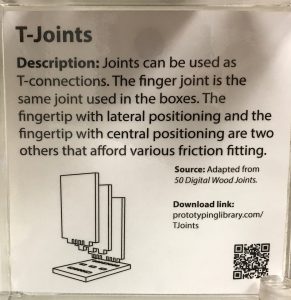
Description of T-Joints in the Prototyping Library. The illustration depicts the first part mentioned, in which all pieces are essentially the same size.
For the laser-cut Prototyping Library, I decided to try and produce the perfect example of T-joints. The unusual thing about this design is that it is ultimately two separate parts; both involve three pieces of wood fit into a fourth piece using different varieties of T-joints, but one part features four wood pieces of the same size, while in the other, all pieces besides the base piece are shortened into little slats. Thus, for each of my two hopefully-perfect examples of T-joints, I was to create two different parts, bringing the grand total of required parts to a shocking and unprecedented four. Rising to meet the challenge, I downloaded the Illustrator file from the online Prototyping Library and prepared to laser-cut.
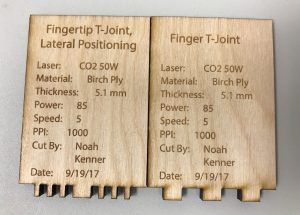
Surviving pieces from the speed 5%/power 85% batch. Even with the laser not fully cutting through the wood in some places, there’s noticeable burning on the bottom and left sides of both pieces.
I began by laser-cutting a few 1-inch squares of wood from the large piece I would use for my models. With each of these squares, I used a different power and speed setting so as to find the optimal combination. Judging from the color of the squares’ edges, as well as the amount of visible burning on each one, I determined that a power of 85% and a speed of 5% was my best bet. However, when used to cut the T-joint file, these settings resulted in the laser not fully cutting through the wood in many places, leading to pieces that were stuck in the wood sheet. I decided not to try and cut the same pieces a second time, as I knew this would inevitably turn their edges to a burnt crisp. Nevertheless, I noticed that the edges already showed slight burn marks, so I needed to adjust the settings ever so slightly so that the laser would fully cut through but the part wouldn’t burn too badly. On the bright side, this iteration showed me that the default raster settings were perfect for etching the required information onto my parts, as the writing was dark, clear, and exhibited no charring.
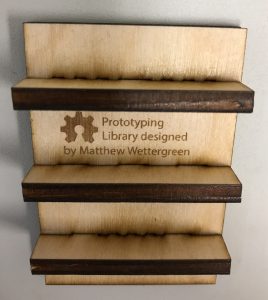
Part from the second iteration, showing the unacceptable level of burning found where pieces join together
For the next cut, I tried keeping the speed at 5% but increasing the power to 90%. This time, the laser cut much more fully and cleanly through the wood, but sure enough, there was substantially more visible burning than before. As shown on the right, the areas surrounding the teeth and holes that comprise the T-joints were particularly susceptible to burn marks. This level of burning was unacceptable, yet I couldn’t simply decrease the power, as this would bring me back to where I began. I resolved to try reducing both the power and the speed, as this would result in the laser having more time to cut into (and hopefully through) the wood, while also using a power low enough that the wood shouldn’t become charred.
In my third attempt, I used a speed of 3% and a power of 70%. This time, the pieces came out much nicer than they ever had before. They had been cut out of the wood cleanly, and all of the edges were a nice maple color. The burn marks were greatly reduced from the previous iteration, but I still hoped to reduce them further. Nevertheless, a problem emerged. Fitting the pieces together was noticeably harder to do than it had previously been. In particular, one type of joint in the design (the Fingertip T-Joint with Central Positioning) was nearly impossible to squeeze together. This led me to realize that the less material that the laser burns away, the harder it is to fit the T-joint pegs into their respective holes. Short of increasing the tolerances of the design’s Illustrator file, I couldn’t reduce the burn marks much further without being unable to assemble the parts. Thus, although my critical eye wasn’t fully satiated, I decided that my third iteration was sufficient to be my final product. After all, nothing is quite perfect, and sometimes the most important part of making something is knowing when to say, “Good enough.”
Below is a picture of my final four parts, two of each type.