Join us as we take you through our journey of creating a “Hulk Smash” tower. For this project, I teamed up with Jordan, and together we brainstormed ideas. Eventually, we settled on a building design featuring a Hulk figurine “smashing” the top of the tower.
2D DRAWINGS
We started with sketches of the design to visualize how the pieces will come together, then moved onto an Illustrator design of the pieces.

Sketch of the tower

Illustrator sketches for tower parts
LOW FIDELITY PROTOTYPE
After we were given the all clear with our design, we proceeded with making a cardboard, low-fidelity prototype of our tower design. This prototype was crucial as it showed us how technically accurate we needed to be. Some issues we encountered with the cardboard model included:
- Making sure the gears were in line with the pushers so it can be caught with each rotation
- The pushers could not be moved which was partly due to the model being made of cardboard so there is greater friction between the pusher and the holes
- The dimensions of our model needed to be taller and wider due to the gears not being able to complete a full rotation because the height was too short
- Needing a square dowel instead of a round dowel for easier placement of gears
- Orientation of the gears needed to be figured out to create the hulk ‘smash’ ripple effect
- Handle size was too long and could not rotate properly (easy fix)

Low fidelity model – 1

Low fidelity model – 2

Gears for low fidelity model
With these design flaws noted down, we made sure to adjust our design for the medium fidelity prototype to accommodate for these issues. We also made a preliminary sketch for the hulk piece at this point and traced over it in Illustrator to prepare for cutting.
MEDIUM FIDELITY PROTOTYPE
Once we were confident on what needed to be adjusted, we then proceeded to make the medium fidelity prototype using laser cut wood. The best thing about this prototype was seeing the gears move with each rotation, although very ruggedly.

Laser cut pieces for medium fidelity model
The initial problem we ran into when beginning this prototype, was that we did not account for the thickness of the wood compared to the cardboard model and so the pushers were too wide to fit through the holes at first. The next issue we encountered was the orientation of the gears, which ended up being changed many times throughout the prototypes, as it did not create the ripple effect we intended for it to create. We also found that we could make the gears slightly bigger so that the ripple effect (when it works) would be larger and more evident. The main issue in this model was that the dowel did not spin smoothly due to the gears knocking into the pusher system rather than pushing it from underneath which was due to the width of the pushers being too short. Additionally, it was still very difficult to know where to place each gear so we decided we would need to further cut out placeholders to ensure the dowel would stay in the same place each rotation so that the gears would be locked in place. All these adjustments were noted down and taken into consideration for our final design.

Medium fidelity model – 1
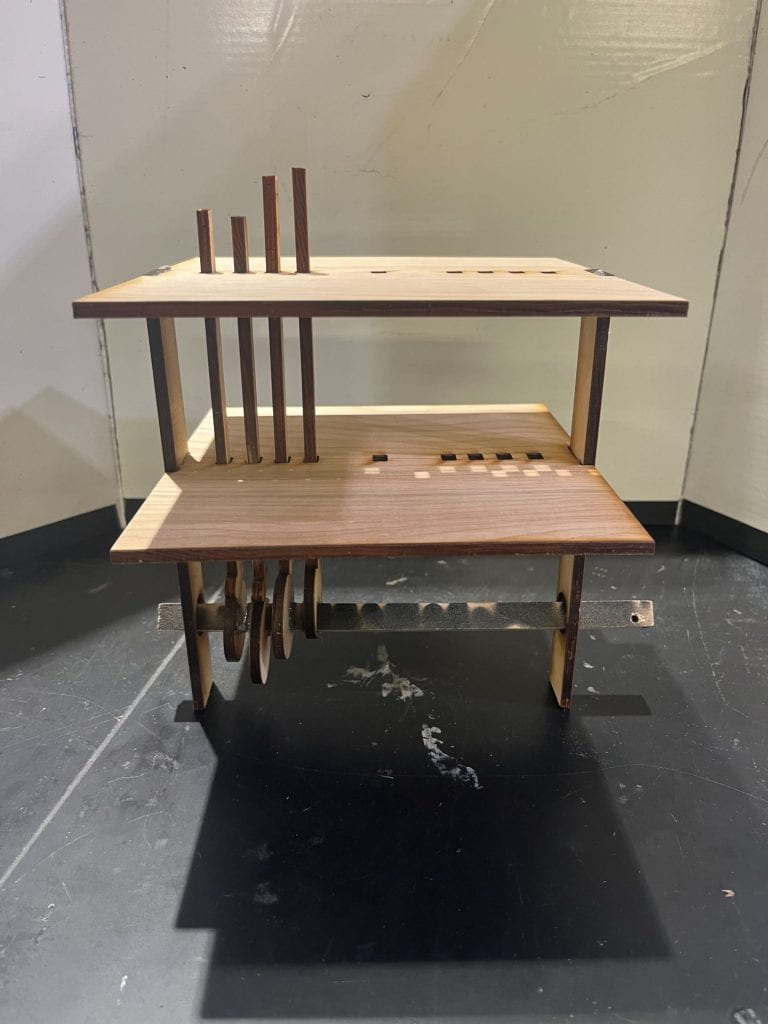
Medium fidelity model – 2
Medium Fidelity Prototype video
HIGH FIDELITY PROTOTYPE
For our final design, we decided to re-cut everything with the laser cutter using masking tape to ensure our parts did not get burnt. We also laser cut the living hinges as the walls of the tower to make the tower come to ‘life’. Additionally, we cut out two ‘explosion star pieces’ for hulk to raise his leg onto to make it seem like he’s stomping into the tower with so much force. Lastly, we cut out a simple name plate including our mechanism number, class, and year. After cutting out everything, we sanded all the edges and the surfaces so that it was smooth. We also did this for the hulk figurine after it was made using the water cutter by sandblasting it first, then filing and sanding the edges afterwards.
Once we were satisfied with the smoothness of the parts, we spray painted each part using a metallic silver for the outer parts to resemble a modern building color, and red for the gears inside the tower to make it stand out. The hulk piece was spray painted green using the vinyl cutter as a mask to cover his shorts and hair for different colors. Unfortunately, there was no purple spray paint for his shorts so we left it clear, and we used black for his hair.

Hulk figurine – spray painted using vinyl

High fidelity model – spray painted parts 1

High fidelity model – spray painted parts 2

High fidelity model – spray painted parts 3
Next we glued all the wooden pieces together using wood glue and we attached the Hulk piece to the “explosion star pieces” with epoxy to secure one of Hulk’s legs to the tower. We initially used a hot glue gun for the other leg, and then switched to epoxy after the first leg had dried to ensure a sturdy bond. The reason we used a hot glue gun was because it would stick the leg to the wood better and hold it in place stronger while the other leg with the epoxy would be left to dry. The glue from the hot glue gun was then removed the next day and epoxy was used in its place to adhere to the requirement that the only glue being used in the final design was only epoxy or wood glue.

Epoxy used to glue hulk figurine to wood
The main issue we encountered during assembly was the difficulty with holding everything in place when trying to glue them together, especially with the wood glue, which took time to set. We fixed this issue by using clamps to hold the pieces in place and to make it level, while we worked on assembling other parts of the tower.

Clamping parts together during assembly
We meticulously planned out the positioning of the gears to make sure it was directly under where the pushers would be. After we assembled the parts together, we both prayed that it would rotate and make contact with the pushers for the entire rotation which it did!

High fidelity model 1

High fidelity model 2
Hulk Smash Demo video (High Fidelity Prototype video)
CONCLUSION
Overall, this was a challenging but fun project that allowed us to showcase all of the skills we have learned and practiced so far in this class. Once we completed the project we reflected on our work and realized that there were things that we could have done differently to make our final product better. One of these things being the application of the wood glue, which was a little sloppy in some areas due to too much being used. We also could have sanded the gears and the pushers for longer to make the motion smoother.
In the end, we were very proud of our design and our ability in managing our time, giving us ample amount of time for any final touches to the design.
COST ANALYSIS
Material Cost:
- Plywood: 1/4″ by 24″ by 24″ $7.28 each from Home Depot
- Aluminum Sheet: $11.47
- Red Paint: $6.48
- Silver Paint: $6.48
- Metal File: $7.99
- Water Jet Cutter: $12.00/hour * 3
- Sand Blaster: $45/hour * 1/4
- Graphic Designing: $19.02/hour * 1
- Personal Labor: $15/hour * 30
- Operating Sandblaster: $19.38/hour * 1/4
- Operating Water jet cutter: $15/hour * 1
Total: $802.52