3D Printing offers the ability to stretch the boundaries of manufacturing. One particularly exciting boundary is that of manufacturing off Earth.
A few years ago, NASA JPL published a blog about the potential to 3d print “fabric” for use as a flexible armor for use in space. While the technology used to make their part (DMLS) is not one we have access to at the OEDK, nor is it something currently practical or safe to use in microgravity, it has inspired numerous variations.
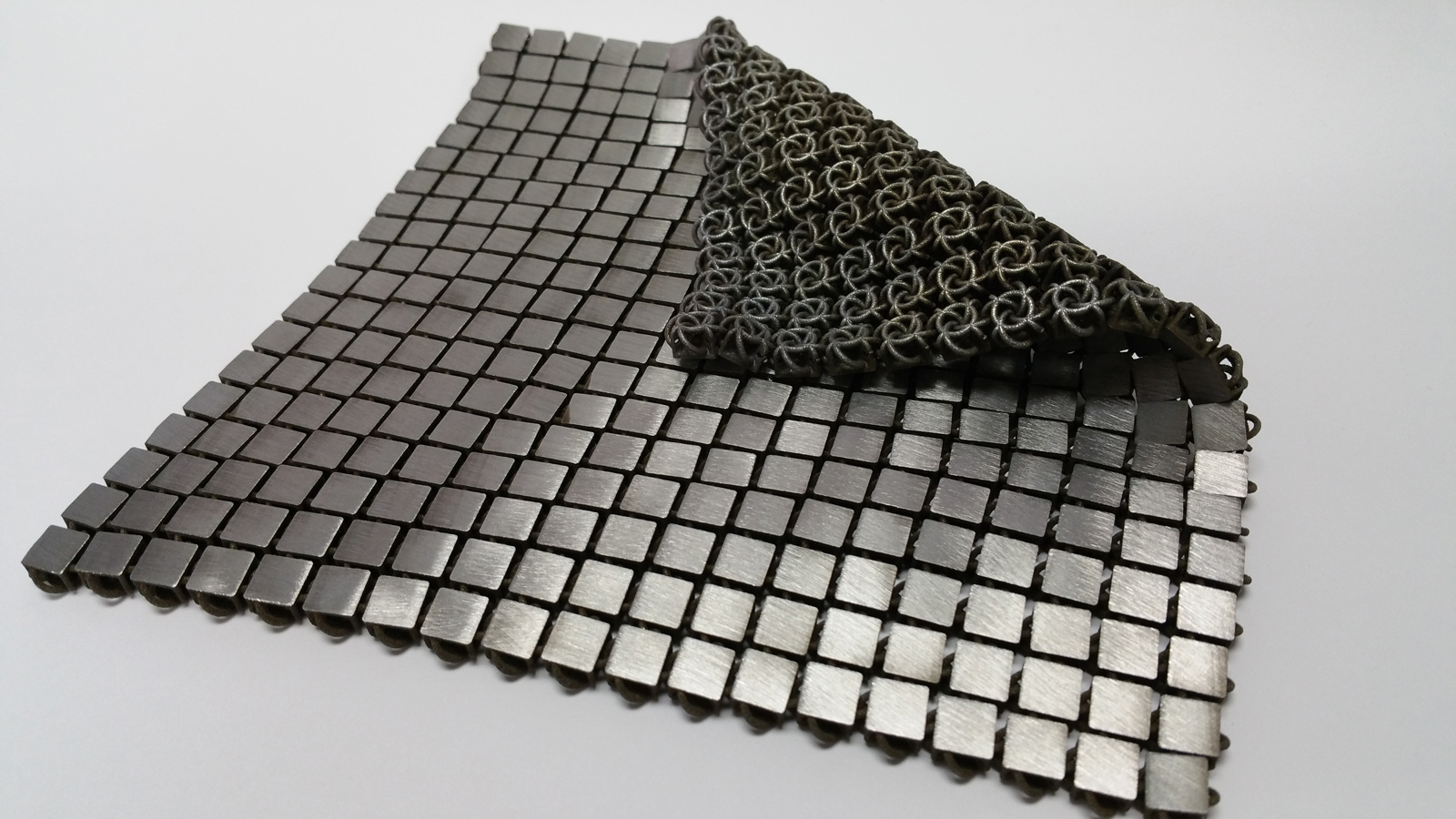
NASA’s 3D printed “fabric”
The NASA design borrows from an idea that has been around for a few thousand years: chain maille. Their design uses a variation on a 4-in-1 link pattern, and the layout requires a powder bed for support of some of the features.
I looked around on various sites like Printables and Thingiverse, and while I found a few designs for FDM, I wanted to try may hand at making one for resin printing. So I fired up Soilidworks and after a few minutes of drawing, had a part that nicely interlocks and has hexagonal pattern for an additional axis of flexibility. I chose self-supporting geometries and the ability to print directly on the bed for better manufacturability.
For my two print methods, I went with two similar resin processes: SLA on the prosumer Formlabs Form 3, and commercial high-production grade DLP (specifically, CLIP) on the Carbon M2.
Other blogs will go into the details of setting up a print, and as that’s a large part of my day job, I won’t go into much detail about setup and printing. I worked to help my partner AJ, who hasn’t had the chance to print much at all, to go through those workflows and it will be covered in more depth on their blog. Both prints came out looking very similar. The geometry was designed with printing in mind, so there weren’t any major issues on either machine. The grey pro scraped off the build platform with some effort, but with care and the proper tools, it came off fine. I used a release film for RPU70 on the M2 as it really sticks to the build platform. Both resins were washed using the wash systems from the respective manufacturers. The Form part needed a bit of additional hand processing to remove the resin. Active person time spent working on both prints was approximately the same. Slightly different tasks, but
The Form 3 printed four parts per build plate in just over 2 hours. The M2 printed five parts in 35 minutes.
As I’m very familiar with the actual steps of 3D printing, I decided to focus this blog on the economics of manufacturing these prints.
A complete Formlabs Form 3+ printer system will run about $3500.
Carbon Inc. will only sell printers to educational institutions–otherwise they only lease their machines. Prices vary, but the printer I used for this would lease to a company somewhere in the realm of $25k a year. Quite the difference. So why would anyone use the Carbon over Formlabs?
I don’t want this blog to come across as a sales pitch for Carbon so I won’t go into extensive detail, but a key differentiation between their systems and others are the resins, and how those are surprisingly affordable.
On the Form 3, I used Grey Pro, a single-part resin that costs $200 per liter.
On the Carbon M2, I used RPU 70, a two part resin that costs $50 per liter at moderate purchase volumes.
I gave each printer a utilization of 8 hours/day, 50 work weeks a year which is arbitrary and almost certainly inaccurate: overnight prints of larger items are common and in a production shop would likely be being used closer to 12 or 16 hours a day, but assuming these very short prints and utilization only during that time lets me give a reasonable comparison. So here are the numbers including some consumables but not PPE and things like towels and waste disposal:
Printer | Cost name | Functional Duration | Cost | Hourly cost | Per unit cost |
Form 3 | Printer | 60 months | $ 3,500.00 | $ 0.006 | $ 0.01 |
Resin tank | 250 hours | $ 150.00 | $ 0.60 | $ 1.20 | |
IPA, 1.5 gal. | $ 26.25 | $ 0.13 | |||
$ 0.34 | |||||
Carbon | M2 | 12 months | $ 25,000.00 | $ 0.042 | |
DPM, Barrel | 2700 washes | $ 1,600.00 | $ 0.58 | ||
$ 0.12 |
Cost Type | Cost | Price | Source | Quantity | Total |
Materials | Grey Pro Resin | $200/liter | Formlabs | 8 mL each | $0.16 ea. |
RPU 70 Resin | $50/liter | Carbon 3D | 8 ml each, 90 mL minimum | $0.04 ea | |
Overhead | Formlabs OH | $0.34 /unit | Calculated | 4 | $1.67 |
Formlabs Depreciation | $0.006 /hr | Calculated | 2 hr | $0.012 | |
Carbon OH | $0.12 /unit | Calculated | 5 | $0.58 | |
Carbon Depreciation | $0.042 /hr | Calculated | .5 hr | $0.021 | |
Design | Prototyping Engineer | $60/hr | OoI rate | .5 hr | $30 |
Lab Tech | $25/hr | Indeed | 2 hr total | $50 |
Fixed Costs for either printer approximately $80, then $25/hour for a technician to run them.
Per Print, Form: $1.68 (+~30 min per item)
Per Print, Carbon $0.61 (+~5 min per item)